These are some pics on the VSAAB - MIG welding subject
MIG = Metal Inert Gas (Carbon Dioxide - CO2)
MAG = Metal Active Gas (80% Argon + 20% CO2 and other mixtures)
MIG/MAG uses a thin wire electrode that is fed to the mouthpiece by a small motor.
The wire melts while welding. The electrode wire may be of stainless and other types of steel.
MIG/MAG welding can be done with one hand.
TIG = Tungsten Inert Gas, uses a fixed Tungsten electrode (Tungsten does not melt) and a
separate rod that is 'dipped' into the molten metal while welding. You need both hands
to do this, one to hold the TIG mouthpiece, the other to hold and dip the rod.
With TIG it is possible to weld aluminium (and aluminum too)
Pictures taken from the German magazine 'Oldtimer Markt' - sonderheft #19' (so the text is in German)
VF Verlagsgesellschaft mbH, Lise Meitnerstrasse 2, D-55129 Mainz, BRD
tel 0 61 31-992-0, fax 0 61 31/922-103
ISSN 0943-7320
MIG/MAG Equipment;
mouthpiece, gas mixture, pressure regulator
electrode/welding wire, transport motor.
power control
sheet thickness/power settings table, interval switch
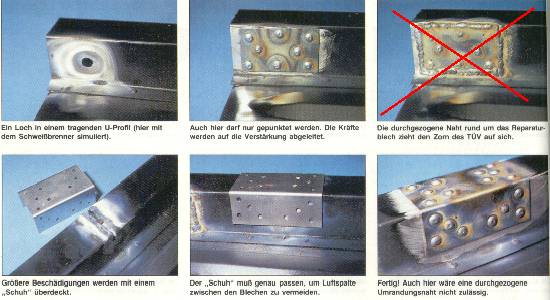
repair of structural (load bearing) parts (scuff plates, inner fenders,
fire wall, shock supports...) may only be done by making spot welds.
repairs by so called 'butt welds' will not pass the
TÜV (annual) safety inspection
long uninterupted butt welds will make the metal brittle, just next to the weld,
actually weakening the repaired spot.
NOT making it stronger!
diameter and distance of spot welds are all subject to (DIN) regulations.

two errors in one,
1 - welds may not be on corners or edges
2 - no butt welds (on structural parts)
an accepted way to repair a structural part is either to replace the entire panel
or to spot weld a repair panel on top of it.
(the example is the inner left front fender of a VW Beetle)

repairs on non structural parts;
cutting a repair piece to size
cutting out the (simulated) rust hole
just slightly larger (1 mm) than the repair piece
spot welding 'tacking' the patch in place
followed by butt welding all around
'cosmetic' polishing the weld to make it flush with the surrounding area,
spray painting, finished!
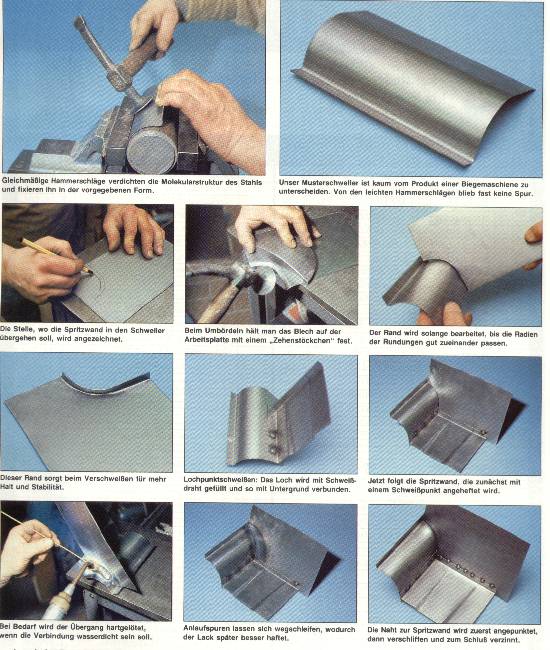
Metal forming -
this is what makes repairs expen$ive !
but it can be a DIY job using simple tools and a lot of practise.
here the seam is brazed (soldered with brass) water tight
it can also be done with a plastic sealer
MH Oct 1999     visitor #